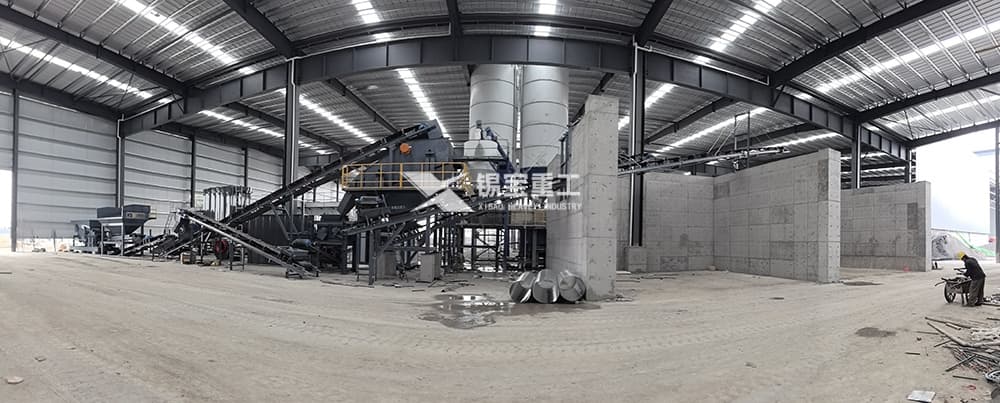
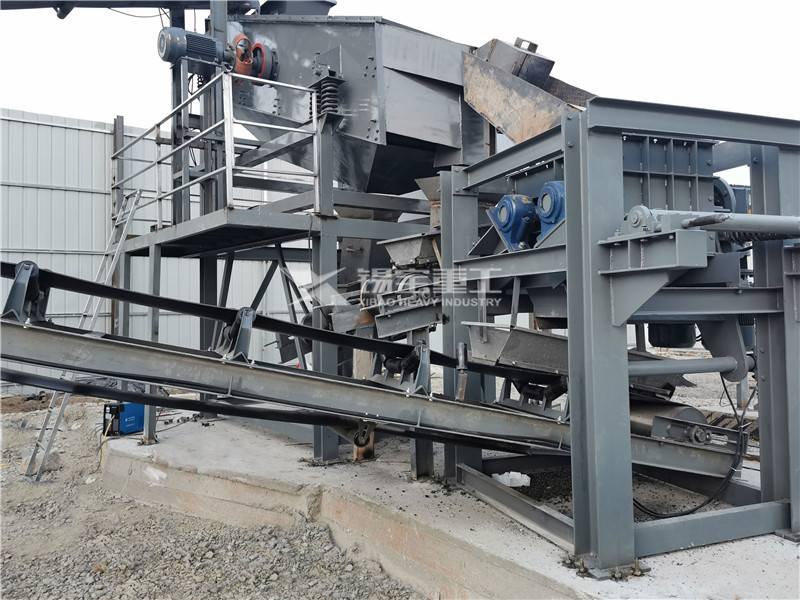
In recent years, road construction has often encountered difficulties in stone procurement and high cost expenditures, which affect the progress of road construction and the cost of the project. Especially for the construction of asphalt concrete pavement, a series of problems such as aging and damage often occur due to prolonged use, which affects the normal use of the road. In order to repair these pavements, asphalt milling and screening equipment is generally used to remove the damaged surface of the asphalt concrete pavement, and then new asphalt concrete is spread to improve the condition of the original pavement.
The installation of asphalt milling and screening equipment needs to be selected in a site with a certain slope to reduce the amount of earthwork work. Therefore, when choosing the model of asphalt milling and screening equipment, everyone should pay more attention to the natural drop height of the equipment installation floor at the feeding port, the shape of the equipment installation floor, and the occupied area of the equipment. The site area of crushing and screening equipment is generally determined based on the installation area of the equipment, the location of feed and discharge ports, the generator room, product specifications and storage capacity, entry and exit of the site, transportation and transportation within the site, warehouse, etc.
The so-called crushing and screening equipment is simply a mechanical equipment that crushes the extracted rock materials under external forces and screens them according to the specifications required by the project. Due to the brittle nature of rock materials, various complex deformations and fractures occur when external forces exceed their compressive capacity. In order to meet the needs of various road construction projects for stone materials, asphalt milling and screening equipment has become an essential auxiliary tool in industrial road construction.
When selecting crushing and screening equipment, it is not only necessary to consider factors such as the size, texture, quality, and content of the stone, but also to clarify the requirements of the engineering equipment, finished product particle size and crushing ratio, and the size of the site. The asphalt milling material crushing and screening equipment is mainly transported by the loader to the recycled material bin, and then transported by the conveyor belt to the screening device. According to the required specifications of the project, the recycled material can directly enter the raw material bin. The remaining raw materials that meet the requirements need to be crushed by the crusher and then enter another raw material bin for use. After crushing and screening, the size and specifications of the stone material are uniform, the structure is simple, and the discharge particle size can also be adjusted according to the project.