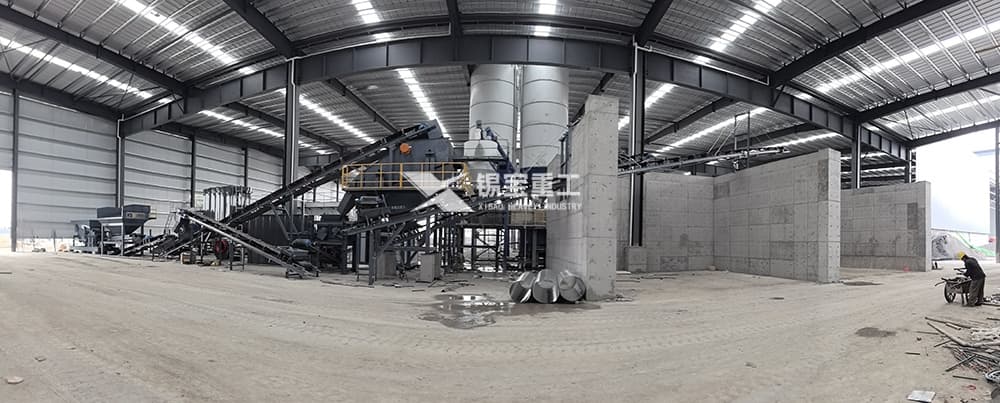
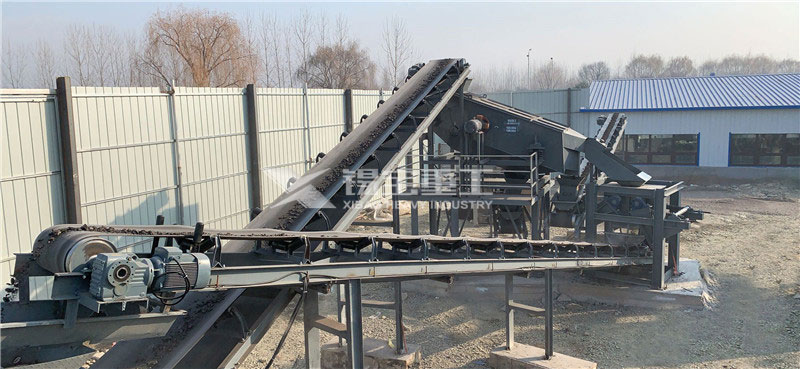
More and more road construction companies, in order to reduce road investment costs, are willing to use waste asphalt crushing equipment to recover waste asphalt pavement, so as to reduce investment costs during road construction.
However, as a road construction company, when choosing, since there are more than one manufacturer like this, in order to ensure convenient and simple use, it is necessary to choose a company with high technical content, stable production performance, and choose according to one's own needs. For example, what is the amount of asphalt recycled material required for daily construction? When selecting equipment, the daily production of waste materials should be greater than the amount of self construction, so that after equipping the equipment, it can keep up with the amount of self construction and not affect the project schedule.
When purchasing waste asphalt crushing equipment, it is also important to consider whether the manufacturer can develop the equipment themselves. The R&D team has strong capabilities and strictly controls every process throughout the entire production process. The equipment is sold directly by the manufacturer, and after-sales service can keep up. Different spare parts are used, and they can be provided in a timely manner when needed for replacement. Manufacturers like this can only purchase with confidence due to their high level of equipment technology, guaranteed quality, high cost-effectiveness, and excellent after-sales service.
In order to improve the service life of waste asphalt crushing equipment, including minimizing malfunctions throughout use, attention should also be paid to maintenance and upkeep. Any equipment that does not pay attention to maintenance and upkeep will reduce the service life of important components, such as bearings, which may not keep up with regular maintenance, resulting in reduced service life and frequent malfunctions. Generally, maintenance and upkeep should be carried out every few months, such as lubrication of friction surfaces, maintenance of different bearings, and external cleaning, all of which must be done properly. And during maintenance, when using lubricating grease, it is necessary to choose high-quality lubricating grease and fill the space inside the bearing seat with 50% lubricating grease. Operating it every 5 months can not only ensure the normal operation of the equipment, but also improve its service life.